120 BPM Blender
SPECIFICATION: PS-FB120
The most technologically advanced blender in the market combines breakthrough controls, modular design and serviceability. It utilizes the PowerServe Vortex™ tub design to ensure a consistent homogeneous blend. The PowerServe Hydraulic Hopper™ – combined with three (3) modular sand screws – provides the simplest, maintenance friendly system along with the most reliable and flexible sand delivery for a variety of job requirements. The FlowServe discharge pump reduces total lifecycle costs and improves productivity, profitability and pumping system reliability.
Specifications
Mixing + Delivery Rates | |
Fluid Rate | 2.0 to 120 bpm at 55 psi minimum discharge pressure |
Sand Delivery Rate | 100 lb/min to 25,000 lb/min |
Sand Concentration | 2.0 ppg sand at 2.0 bpm 20.0 ppg sand at 55.0 bpm 5.0 ppg sand concentration at 120 bpm |
Two (2) modular hydraulic power units will be used on the blender. Each will be powered by US EPA Tier compliant diesel engines. Customer option on engine make between:
Engine Option 1
- Cummins QSX15
Rated Output Power:
- 600 BHP
Engine Option 2
- Caterpillar C15
Rated Output Power:
- 580 BHP
Engine Option 3
- MTU Detroit Diesel
Rated Output Power:
- 660 BHP
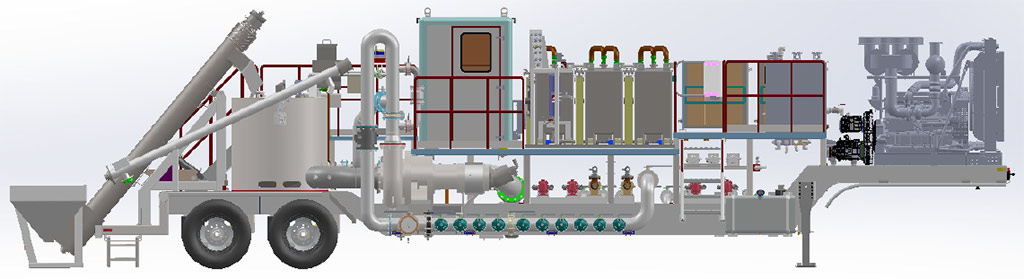
GEARBOX
Durst 4PD11D
SUCTION PUMP
Gorman Rupp
- Model: 612L20-B/S2
DISCHARGE PUMP
Flowserve Slurry Pump
- Model: 10M234
HOPPER AND SAND SCREWS
The sand screws are designed to be modular to allow quick removal and configuration. The design incorporates the following features:
- Common collection hopper for 3 screw assemblies
- Standard flight screws
- Top drive hydraulic motors (Eaton ME Series) for closed loop hydrostatic drive motor
- Magnetic pickup with 120 tooth sprocket for speed sensing
- Screws lowered/raised with hydraulic lift cylinders with mechanical storage latch
- Available Sizes & Rates:
- 6” – 160 to 2,500 lb/min
- 9” – 400 to 6400 lb/min
- 12” – 740 to 12,000 lb/min
DRY ADDITIVE SYSTEM
Up to two (2) dry additive feeders can be mounted on the blender. The feeders discharge into a mixing eductor that discharges directly into the mixing tub.
LIQUID ADDITIVE SYSTEM
Liquid additive chemicals are metered into the slurry at different points in the process. Onboard tanks are used to store additives. Chemical transfer pumps are used to fill the onboard tanks for fluid sources external to the unit. The LA system is completely customized by the customer.
TANKS
- Quantity: Up to 5
- Capacity: 100 gallon
- Construction: 316 stainless steel
CHEMICAL TRANSFER PUMPS
- Quantity: Up to 5
- Rate: 15 gpm
LIQUID ADDITIVE PUMPS
- Quantity: Up to 8
- Mounting: Universal base for quick and easy pump swap out
POWERSERVE VORTEX™ MIXING TUB
PowerServe Vortex™ mixing tub has a unique proprietary design that utilizes the clean fluid entry flow to increase the mixing agitation in the tub.
- Clean Fluid Inlet: 8” Victaulic entry
- Discharge Outlet: 12” Victaulic bottom sump
- Mixing Nozzles: 3 rows, eight (8) 2” nozzles, staggered row spacing
- Tub Diameter: 60 inches OD
- Tub Volume: 12 bbl
PROCESS MANIFOLD
The blender is configured with the suction header on the road side of the unit and with the discharge header on the curb side of the unit. The suction and discharge headers are equipped with a crossover. Both headers are equipped with sectioning valves to isolate portions of each header.
- Discharge Connections:
- One (1) 8” hose connection Fig. 206 female union (thread) with chained cap
- Ten (10) 4 inch Fig. 206 female union (thread) with chained caps
- Suction Connections:
- One (1) 8” hose connection Fig 206 female union (thread) with chained cap
- Twelve (12) 4 inch Fig. 206 male union half (wing) with plugs
CONTROL CABIN
- Construction: Custom aluminum control cab
- Dimensions: 58” L x 58” W x 84” H
- Air Conditioner: Wall mounted
- Electrical components/systems only in control house (no hydraulics or pneumatics in cab)
- Kick-out emergency window
CONTROLS
- The R-Blend™ control system provided by Raptor Oilfield Controls is standard. Other control systems may be supplied upon request.
- System: PC based automatic control system
- Type: Parker electrohydraulic valves
- 4–20 mA signals for proportional controls
- 24 VDC system
LIGHTING SYSTEM
System:
- Work lights are mounted at various locations on the unit to illuminate the unit work zones and surrounding area. Lighting is powered from the deck engine 24 volt system.
240 BARREL GEL HYDRATION
SPECIFICATION: PS-GEL 240
PowerServe Hydration units deliver a consistent homogenous gel using the proprietary PowerServe High Shear Mixing System™. The mixing system puts more shear into the gel than conventional paddle mixing systems. The 240 bbl hydration tank with torturous path baffling insures adequate hydration time with a first in/first out fluid path.
Specifications
Unit Dimensions | |
Length | 49’ (overall) 41’-5” (kingpin to bogey) |
Width | 8’-6” |
Height | 13’-2” (mounted on 52” high fifth wheel) |
One (1) hydraulic power unit will be used on the unit. The HPU will be powered by a US EPA Tier compliant diesel engine per following specifications. Customer option on engine make between:
Engine Option 1
- Cummins QSX15
Rated Output Power:
- 600 BHP
Engine Option 2
- Caterpillar C15
Rated Output Power:
- 580 BHP
Engine Option 3
- MTU Detroit Diesel
Rated Output Power:
- 660 BHP
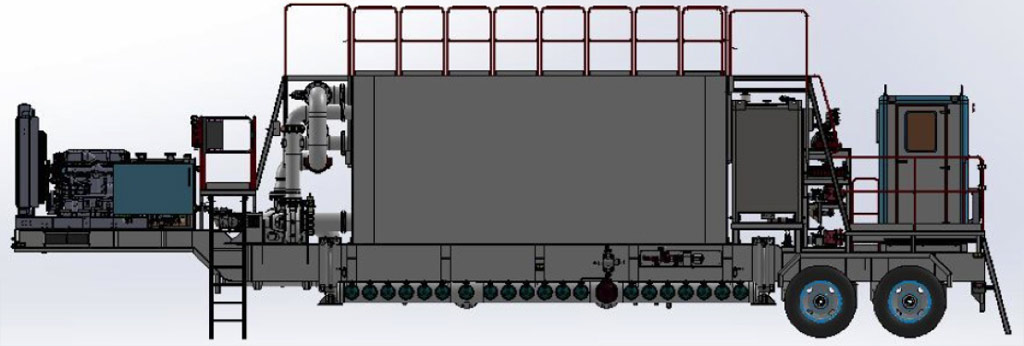
GEARBOX
Durst 4PD11D
SUCTION PUMP
Gorman Rupp
- Model: 612L20-B/S2
RECIRCULATION PUMP
Gorman Rupp
- Model: 610M20-B
LIQUID ADDITIVE SYSTEM
Liquid additive chemicals are metered into the suction piping immediately before the suction pump. Onboard tanks are used for storing LGC for low rate jobs. The liquid additive pumps meter the chemicals into the process piping at precise ratios. The LA system is completely customizable to meet specific customer needs and preferences.
LIQUID ADDITIVE TANKS
- Quantity: Up to 2
- Capacity: 550 gallon
- Construction: Stainless steel construction
LIQUID ADDITIVE PUMPS
- Quantity: Up to 6
- Types:
- Lobe pumps – Waukesha, Ampco
- Progressive Cavity – Roper, Tarby
- Other pump types and manufacturers can be accommodated based upon specific customer requests.
- Mounting: Universal base for quick and easy pump swap out
- Chemical resistant hoses from LA pumps to connections on inlet of suction pump piping
HYDRATION TANK
- Carbon steel construction with internal corrosion resistant lining
- Transverse torturous path baffling
- 240 bbl volume
- Recirculation shear mixer
LIGHTING SYSTEM
Work lights will be mounted at various locations on the unit to illuminate the unit work zones and surrounding area. Lighting will be powered from the deck engine 24 volt system.
PROCESS MANIFOLD
The unit is configured with a header arrangement that can take suction or discharge from either side of the unit. The headers are equipped with isolation valves to allow the operator to recirculate external frac tanks.
- Construction: Schedule 40 steel piping
- Connections (per side):
- One (1) 8” Fig. 206
- Twenty (20) 4” Fig. 206
- Custom arrangements of 4” & 8” connections can be made upon request
- Hydraulic actuated valves on all crossover valves
HYDRAULICS
- 110 gallon custom tank with in-tank filters
- ASA hydraulic cooler
- Sundstrand-Sauer Series 90 hydrostats for centrifugal pumps
- Parker P3 Series open loop pump
- Tub Level: Parker D1FH directional proportional valves
- LA Pumps: Parker D1TX directional proportional valves
- Misc. Valves: Parker
CONTROL CABIN
- Construction: Custom aluminum control cab
- Dimensions: 66” L x 54” W x 84” H
- Air Conditioner: Wall mounted
- Features:
- Electrical components/systems only in control house (no hydraulics or pneumatics in cab)
- Kick-out emergency window
CONTROLS
- The R-Blend™ control system provided by Raptor Oilfield Controls is standard. Other control systems may be supplied upon request.
- System: PC based control system
- Type: Parker electrohydraulic valves 4 – 20 mA signals for proportional controls
- 24 VDC system
INSTRUMENTATION
- Viscometer: TT100 Brookfield
- pH sensors: Endress Hauser pH sensor
- Clean flow meter: Rosemount magnetic flow meter
- LA flow meters: Micromotion coriolis mass meters
- Tub level: Rosemount guided wave radar